Poor metallurgical conditions and fierce competition
Few industries can compare with the harsh working conditions of steel and other metal plants. Temperature and speed limits. Heavy and continuous impact load. Grinding dust, corrosive chemicals and high humidity. The combination of these conditions will degrade the equipment and cause unplanned shutdown. Even under good conditions, effective maintenance will become difficult.
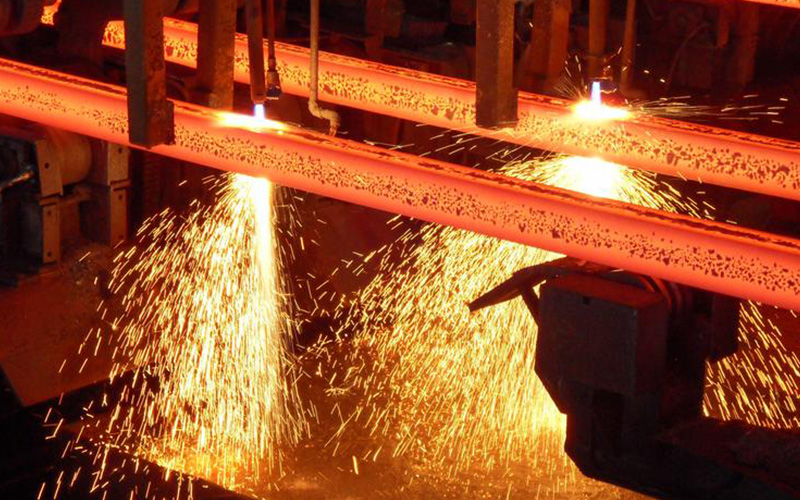
Metallurgical solutions can help
Expertise in bearings and bearing units, seals, lubrication systems, mechatronics and services can provide unique system solutions for upstream and downstream applications.
The tools and technologies provided include life cycle management, which is an effective method to reduce the total cost of equipment at each stage, including all stages from technical parameters and design to operation and maintenance. The solution provided helps the factory:
Increase output
Reduce unplanned downtime
Reduce operating costs
Improve product quality
Reduced maintenance
Reduce environmental impact.
Improve safety production;
Equipment upgrading
Metallurgical industry, application, case and scheme
Upstream - steelmaking
In view of the rising demand and competition for steel, steel mills are now seeking a way out to optimize the agency and save the cost per ton of steel. This is a major challenge given the harsh environment in which materials are transported in the factory.
Upstream solutions help factories convert raw materials into molten steel, making the process more stable, cost-effective, high-quality, safe and reliable.
Upstream - continuous casting
In view of the rising demand and competition for steel, the continuous casting agent line is under great pressure to optimize the agent and save the cost of metric tons. Many steelmakers try to stand out by improving process control, improving product quality and acting as agents to update products with higher steel grades.
In the process of operation, the continuous casting agent line is faced with a series of conditions that make it difficult to improve the process and products. Frequent and expensive shutdowns for maintenance are unavoidable, because water, mold powder and scale will enter the bearing pedestal.
With decades of experience in the industry, the solution helps customers reduce maintenance costs, enhance process control and improve the agent rate of the continuous casting agent line.
Upstream - rolling mill
While maintaining and improving product quality, hot rolling mills and cold rolling mills are facing the pressure of increasing output. This usually means adjusting the equipment to accommodate heavier loads or reconfiguring the mill stands, which is an expensive recommendation.
In both cases, the characteristics of process control make the working conditions and maintenance requirements of bearing configuration more severe. The operation safety and environmental protection legislation has increased the challenge difficulty.